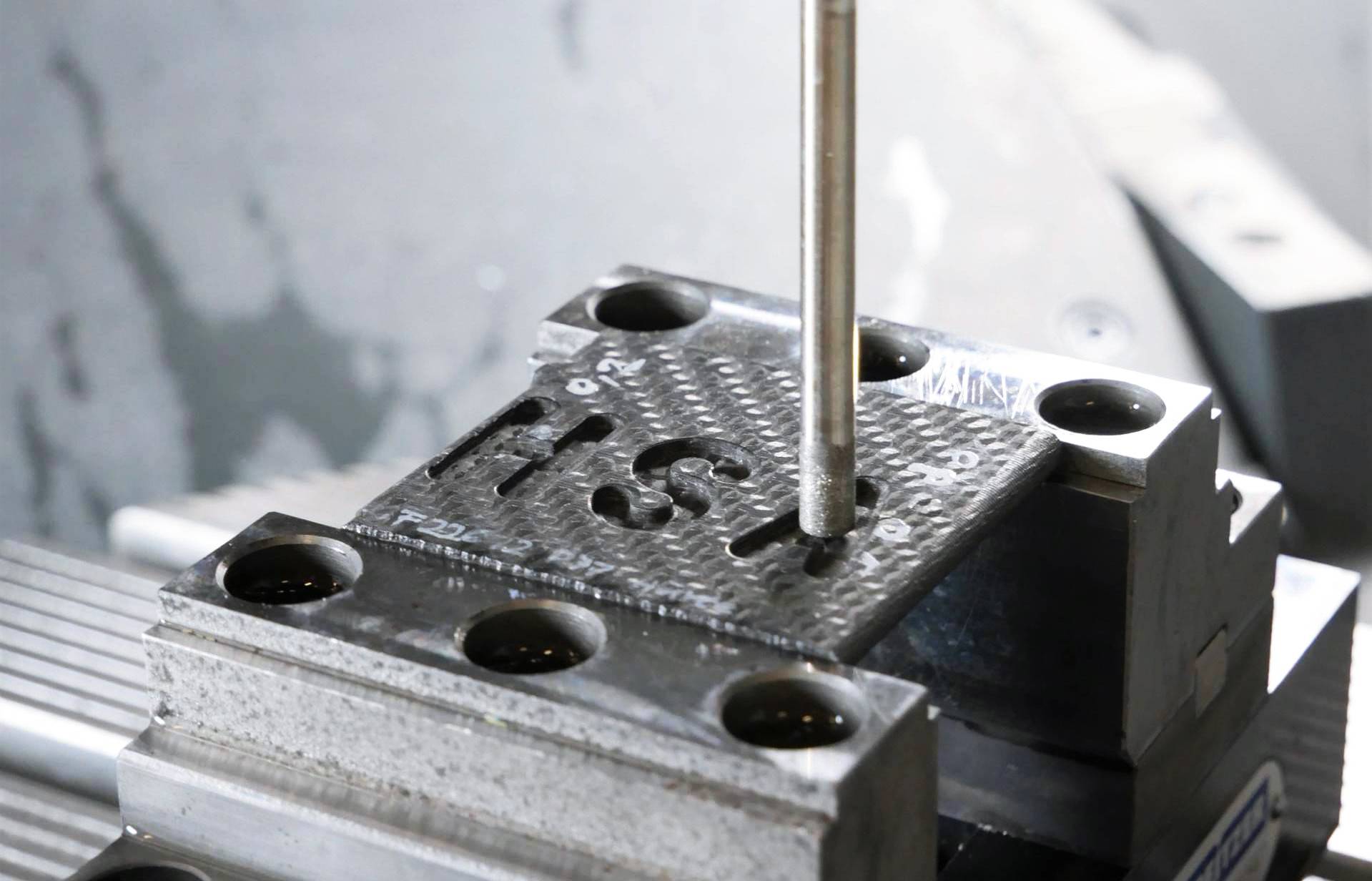
The future of Cutting
01.01.2020
Im Projekt ULTRACUT der THA_comp wird ein innovatives, ultraschallgestütztes Hybridverfahren bei der Zerspanung von Faserverbundkeramiken untersucht. Der Forschungsschwerpunkt liegt auf der Prozess- und Werkzeugauslegung zur Entwicklung eines optimierten Prozesskennfelds für eine stressreduzierende und ressourcenschonende Bearbeitung im Vergleich zu konventionellen Verfahren ohne Bearbeitungsqualitätsverlust. Dabei werden die prozessentlastenden Effekte dieser Technologie auf das Materialabtragverhalten sowie auf Qualitäts- bzw. Prozesskenngrößen analysiert. →